デジタルツインとは?DXとの関係や今後の課題、活用事例についても紹介
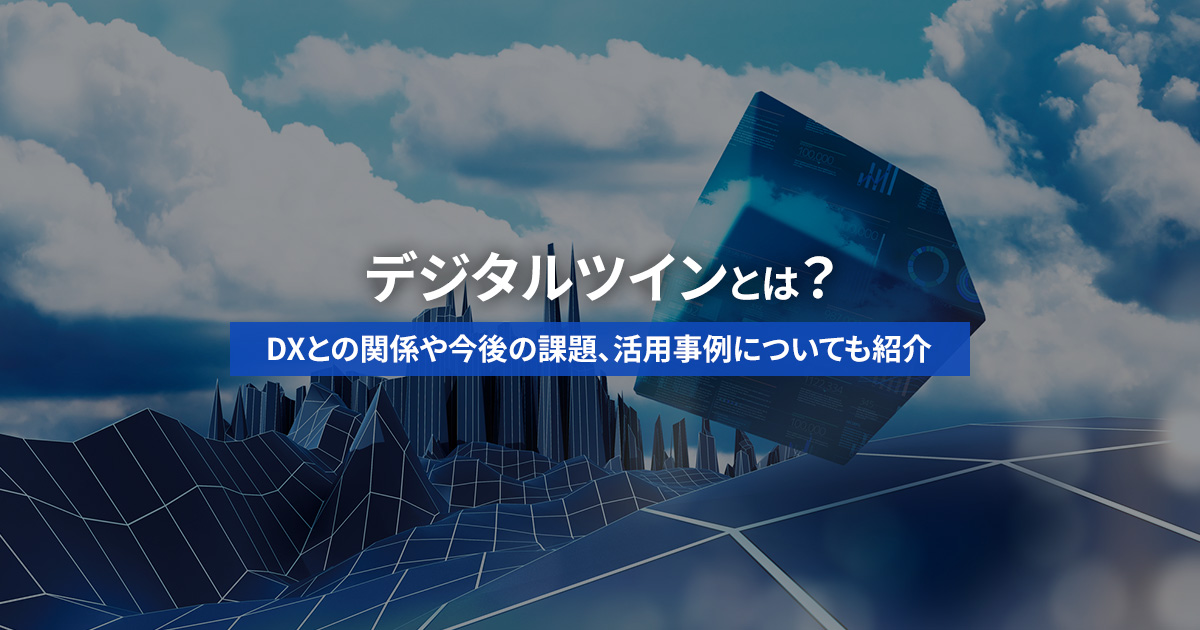
IT技術は急速に進歩しており、現実空間だけでなくサイバー空間での活用も進み始めています。しかし、サイバー空間に現実空間を再現する「デジタルツイン」という言葉を聞いたことがある方は、それほど多くはないかもしれません。
この記事では、デジタルツインの概要やDXとの関係性、活用事例や今後の展望などを解説します。
目次
デジタルツインとは
デジタルツインとは、デジタル技術を用いてサイバー空間上に現実空間を再現することを指します。2002年に米ミシガン大学のマイケル・グリーブス教授によって提唱された概念です。ツイン(twin)という言葉は双子や2対という意味を持つ英語ですが、その名の通り、現実空間と対になる空間を、デジタル技術を活用してサイバー空間上に作り上げることを意味しています。
デジタルツインの仕組み
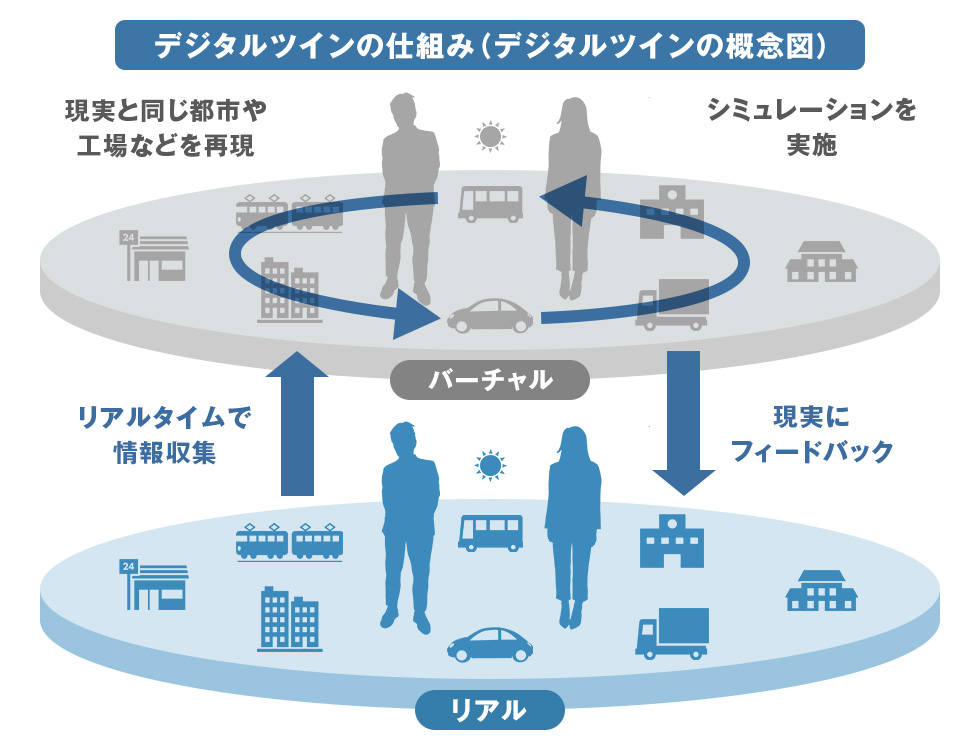
デジタルツインは、現実空間に設置されたセンサーやカメラといったIoT機器で取得したリアルタイムデータをサイバー空間上に反映することで実現されます。取得したリアルタイムデータはAIによって分析・処理され、現実空間の環境がリアルに再現される仕組みです。
このデジタルツインで再現したサイバー空間を用いれば、現実空間では検証が難しいシミュレーションが可能となり、より実践的なフィードバックを得ることができます。
DXとの関係
DX(デジタルトランスフォーメーション)は、データやデジタル技術を活用して新しい価値を創出する取り組みを指しますが、デジタルツインもDXの取り組みの一部といえます。
デジタルツインは、IoT機器などで取得したデータを活用し、現実空間に即した実践的な検証環境を作り上げる取り組みです。デジタルツインの実現にはデータ以外にもさまざまなデジタル技術が必要となるため、一朝一夕で行えるものではありませんが、DXのなかの大きな施策として、今後多くの企業で求められる取り組みとなるでしょう。
DXについては以下の記事で詳しく解説しています。
インダストリー4.0との関係
インダストリー4.0は、モノづくりの現場でデータやデジタル技術を活用し、製造プロセスの改善や新しいプロダクトの創出などを実現する取り組みです。このインダストリー4.0においても、IoT機器などを使って取得したビッグデータをAIで分析・処理する取り組みが必要になります。成果物はそれぞれ違いますが、実現までのプロセスには共通する部分が多くあります。
インダストリー4.0については以下の記事で詳しく解説しています。
デジタルツインに必要不可欠な技術
デジタルツインの実現には、下記のような技術が必要になります。
- IoT
- AI
- AR、VR
- 5G
IoTはセンサーやカメラが得た現実空間のデータをリアルタイムに取得するための技術で、IoT機器などから得られたデータをAIで高速に分析・処理することでリアルタイムにサイバー空間を構築しています。サイバー空間上で物体を再現するためにはAR(拡張現実)やVR(仮想現実)の技術も必要ですし、リアルタイムに取得したデータを低遅延で伝送するための5G回線も必要不可欠です。
シミュレーション・メタバースとの違い
デジタルツインと混同されやすい概念に「シミュレーション」や「メタバース」があります。それぞれの違いを見ていきましょう。
シミュレーション
シミュレーションとは、特定の事象を模擬的に実践・再現しフィードバックを得ることを指します。必ずしもサイバー空間やデジタル技術が用いられるわけではなく、リアルタイム性や実践・再現方法の範囲が定まっているわけではない点が、デジタルツインとの違いです。
ただしシミュレーションには、データやデジタル技術を活用したもの、リアルタイム性を持たせたもの、サイバー空間で実践・再現するものも手法に包括されるため、デジタルツインはシミュレーションの一部だともいえるでしょう。
メタバース
メタバースとは、サイバー空間上に作り上げた仮想的な空間そのものを指します。デジタルツインは実践的なフィードバックを得るために現実空間を再現する必要がありますが、メタバースは必ずしも現実空間を再現する必要はありません。
また、メタバースはサイバー空間を通して物理的な制約を取り払ったコミュニケーションを可能にすることが主流となっており、デジタルツインと利用目的が異なります。
デジタルツインが注目されるようになった背景
デジタルツインは2002年に提唱された概念であり、さらにその元となる概念は1960年代から存在していたといわれています。それが近年になって注目を集めるようになった理由は、技術の発展により低遅延でデータ伝送が行えるインターネット環境が整備されたこと、IoTやAI、AR/VRなどによって現実空間の再現度が向上したことにあります。
現時点では企業単体としてデジタルツインを実現することは難しいですが、デジタルツインの実現で得られる効果は大きく、さまざまな業界での活用が期待されています。
デジタルツインのメリット
デジタルツインの実現によって得られる主なメリットは主に以下の5つです。
コストの削減
デジタルツインの実現はコスト削減に繋がります。例えば製品開発を行う場合、製品の評価には実際に製品の作成が必要です。一方、サイバー空間ではデータさえあれば製品を安価に再現できます。
同じようなモデルをベースにした製品があれば、その製品をカスタマイズし再現することも容易であり、安価かつ効率的に製品開発できるようになります。
業務の効率化
デジタルツインを実現できれば、製造現場での業務や状況を高精度で可視化できます。可視化した業務に対して改善施策を投入すれば、改善効果を検証することもできるでしょう。
結果として、効果の高い改善施策の実行に繋がり業務の効率化が実現します。
リスクの回避や軽減
デジタルツインで作り上げたサイバー空間では、ローリスクでさまざまな検証ができます。それにより、製品開発の失敗を防止する、機械が故障した場合の損失額を算出して対策を検討するなど、リスクの回避や軽減を図る行動が取りやすくなります。
また、サイバー空間上にはリアルタイムなデータが反映されるため、生産設備の予知保全の効果も得られるでしょう。
品質の向上
品質の検証や改善には、製品に対してさまざまな試験を行う必要があります。しかし、試験を行う際に新しい製品を使っていてはコストがかさみ、それが原因で品質低下が発生するケースも少なくありません。
サイバー空間で製品の検証や改善を行えれば、適切な試験の実施がスムーズにでき、品質の向上に繋がります。
技能の継承
製造業においては、職人の高齢化と技能継承の停滞が大きな課題となっています。しかし、デジタルツインが実現できれば、サイバー空間上で物理的な制約に縛られずに作業支援が行えるほか、作業内容がデータとして蓄積されるため、教育や技能継承の効率化が図れます。
製造業における技能継承の対策については以下の記事で詳しく解説しています。
デジタルツインの活用事例
ここからはデジタルツインを実際に活用した事例を紹介します。
事例1・航空機製造
航空機を製造するA社では、航空機のエンジンブレードをデジタルツインで再現し、時間経過による損傷予知に活用しています。航空機のエンジンはサイズが巨大なため交換などの対応が容易ではなく、多額のコストがかかります。しかし、デジタルツインによって損傷予知ができるようになったことで、過剰なメンテナンスの削減に繋がり、大幅なコスト減に成功しました。
事例2・化学製品製造
化学製品を製造するB社は、製造プラントにデジタルツインの技術を活用し、ベテラン技術者がどこにいても支援できる体制を作っています。プラントによってベテラン技術者の人数に差がある場合、異常が発生した際に対応ができないという状況に陥る可能性があります。
そこでデジタルツインを活用し、異常発生時に現場にベテラン技術者が居なくても、遠隔で出向き対応できるような体制作りを進めています。
事例3・ITベンダー
SCMを提供するITベンダーC社は、製造業のサプライチェーンをデジタルツインで再現しました。サプライチェーンにおけるプロセス改善には多くの時間がかかり、マクロ環境の変化を受けやすいという課題があります。デジタルツインによってサプライチェーンの検証を行うことで、低コスト・短期間で最も利益の高い販売・生産計画・輸送ルートなどを発見できるようになり、製造業におけるサプライチェーン改善を実現しています。
デジタルツインの課題や今後について
デジタルツインの実現によって得られるメリットは多いものの、さまざまなデジタル技術を駆使するため、企業単体では実現が難しいという課題があります。また、ITベンダーが提供するサービスを利用するにせよ、データの統合や膨大なデータの管理が必要となります。
しかし、このまま技術の進展が進んでいけば、デジタルツインがより低コストで実現できる時代も夢ではなくなるでしょう。さまざまな分野で活用できる技術であるため、今後は市場規模の拡大や製造業以外の分野での活用に繋がる可能性もあります。
まとめ
デジタルツインは、現実空間では実施が困難な検証を低コスト・短期間で実現できる有効な技術です。複合的なデジタル技術の活用やデータの統合・管理における課題があり、すぐに一般化することが難しい側面もありますが、デジタルツインで得られるメリットの大きさや汎用性の高さから、今後一般化していく可能性は十分にあります。
デジタルツインの実現に向けてデータを収集する、デジタルツインの動向にアンテナを張っておくなど、準備を進めておくと良いでしょう。