リードタイムの意味とは?納期との違いや短縮する方法について解説
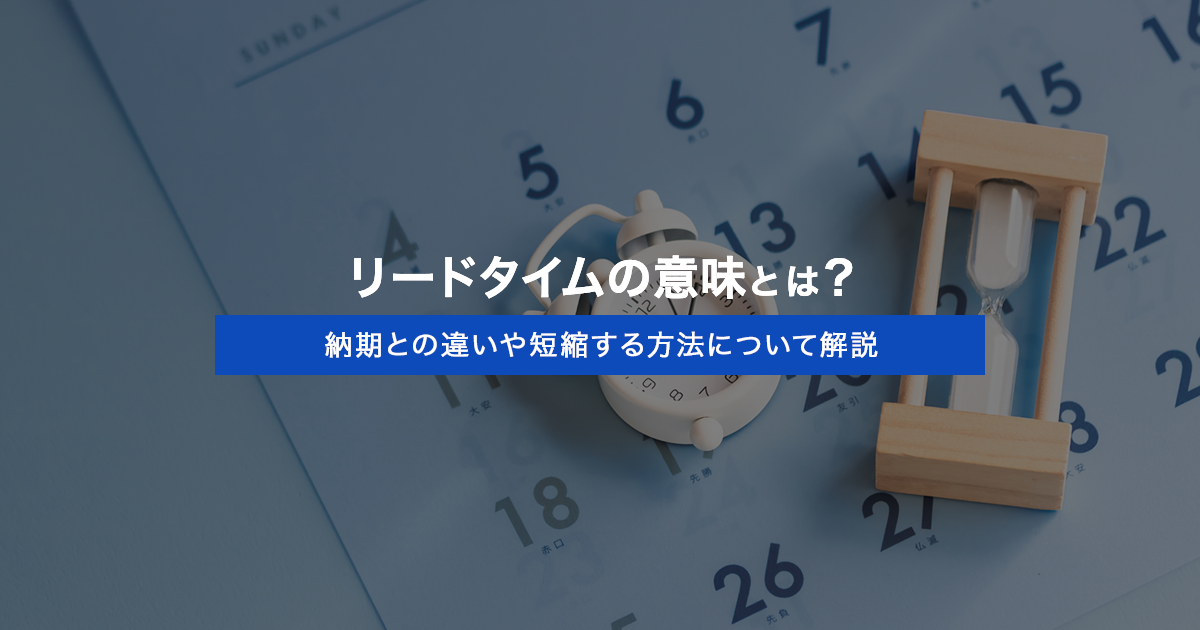
製品の開発から納品までにかかる日数を最適化するためには、リードタイムの管理が欠かせません。しかし、リードタイムにはいくつかの種類があります。それぞれに適切な管理が求められますが、一部しか管理できていないという企業も多いのではないでしょうか。
この記事では、リードタイムの概要と種類、リードタイムを短縮する方法について解説します。
目次
リードタイムとは
リードタイムとは、各工程の始まりから終わりまでにかかる期間を指します。一般的には製品の開発から納品までにかかる期間として用いられ、各工程で細分化される場合もあります。
納期との違い
納期とは、製品やサービスを納品する期日を指します。リードタイムと混同される場合がありますが、リードタイムは「納品までにかかる期間(〇日間)」、納期は「納品する日時(〇月〇日)」を表すのが一般的です。リードタイムを踏まえて設定された納品日時が納期であると考えると良いでしょう。
タクトタイム・サイクルタイムとの関係性
リードタイムに関連する言葉として、タクトタイムやサイクルタイムがあります。
タクトタイムとは、製品一つを生産するのにかけられる時間です。「稼働時間÷必要生産数」で割り出し、必要生産数を達成するためにどれぐらいのペースで生産を行えば良いかを考える際に用いられます。
一方、サイクルタイムとは、製品一つを生産するのにかかる実時間です。「稼働時間÷実際の生産数」で割り出し、計算通りに必要生産数を生産できているかをチェックする際に用いられます。
タクトタイム(長)>サイクルタイム(短)の関係にあれば、必要生産数以上の生産能力がある状態、サイクルタイム(長)>タクトタイム(短)の関係にあれば、必要生産数を生産するだけの生産能力がない状態にあることになります。
リードタイムはタクトタイムやサイクルタイムの影響を大きく受けます。もし生産能力が十分であればリードタイムの短縮に繋がりますし、不十分であればリードタイムは長くなるでしょう。リードタイムの短縮を図る場合には、タクトタイムやサイクルタイムに着目して改善を図ることが重要です。
リードタイムの種類やそれぞれの意味
リードタイムにはさまざまな種類があり、業種や工程などによって用いられるリードタイムが異なります。代表的なリードタイムの意味や範囲を解説します。
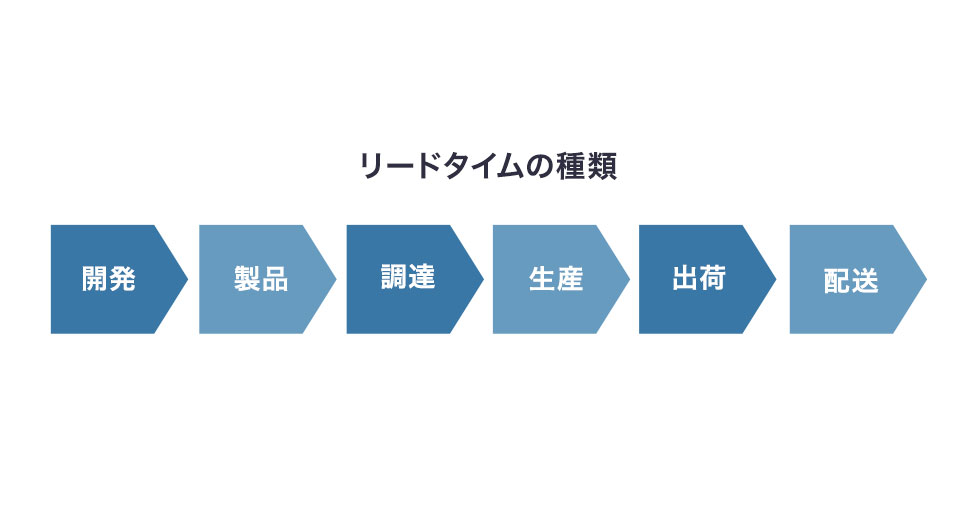
開発リードタイム
開発リードタイムは、製品や技術の企画立案から設計、開発、実用化準備までのプロセスにかかる期間を指します。製造業であれば、製品を生産できる体制を構築するまでが開発リードタイムの範囲であり、既に生産体制が確立されている場合には開発リードタイムは発生しません。
製品リードタイム
製品リードタイムは、製品の受注から出荷までにかかる期間を指します。生産活動における全プロセスにかかる期間はトータルリードタイムと呼ばれますが、トータルリードタイムから出荷以降のプロセスを取り除いたものが製品リードタイムにあたります。
調達リードタイム
調達リードタイムは、原材料の調達にかかる期間を指します。原材料を調達するまでには、発注や輸送、搬入、受入検査などのプロセスが含まれ、これらの調達にかかるプロセスがすべて完了するまでが調達リードタイムです。
発注から納品までの納品リードタイム、納品から受入までの受入リードタイム、受入検査期間の検査リードタイムと細分化して用いられる場合もあります。
生産リードタイム(製造リードタイム)
生産リードタイム(製造リードタイム)は、生産開始から製品ができるまでにかかる期間を指します。製品完成までに複数の工程や作業が存在する場合には、工程ごとの工程リードタイムや作業ごとの作業リードタイムに細分化して用いられる場合もあります。また、単に製品の生産時間だけではなく、品質検査にかかる日数も含まれます。
出荷リードタイム
出荷リードタイムは、製品の受注後に出荷指示を行ってから実際に出荷が完了するまでにかかる期間を指します。出荷業務には、ピッキングや検品、梱包、出荷処理などのプロセスがあります。
配送リードタイム
配送リードタイムは、製品の出荷後、納品先に製品が届くまでの期間を指します。輸送の手段には車、船舶、飛行機などさまざまありますが、それぞれ輸送可能な物品や輸送完了までの日時が異なります。配送物品や配送先によって最適な配送ルートが異なる点は注意が必要です。
リードタイムを短縮するメリット
では、リードタイムの短縮を図ると、どのようなメリットが得られるのでしょうか。
管理コストの削減に繋がる
リードタイムを短縮し、必要なタイミングで柔軟に在庫量を調整できるようになれば、受注に備えて抱えている在庫の量を削減できます。
たとえば、製造にトータルで一ヵ月かかる製品であれば、一ヵ月分の受注量に耐えうる在庫を抱えておく必要があります。それが半月で製品を製造できるようになれば、抱える在庫は半月分で良くなるでしょう。
在庫量を削減できれば、在庫管理コストが削減でき、保管期間の長期化による品質劣化の防止にも繋がります。
販売機会損失の減少に繋がる
近年はAIを活用した受注予測も行われていますが、受注量を完璧に予測することはできません。突発的に受注が増え、在庫量をオーバーすることもあるでしょう。
しかし、リードタイムを短縮しておけば、突発で受注量が増加した場合でも対応がしやすくなり、機会損失を減らすことができます。
業務の効率化が図れる
リードタイムの短縮を図る際、一つひとつの工程を見直していけば、工程の現状把握や問題点の洗い出しができます。洗い出した問題点を改善すれば、業務の効率化が実現するでしょう。
また、一つの工程におけるリードタイムが短縮されることで、その工程の完了待ちが発生していた工程のリードタイムも短縮されるなど、複数工程の効率化に繋がる可能性もあります。
売れ残りや不動在庫の発生を防げる
近年は顧客のニーズが変化するスピードが早まっており、ニーズを超えた大量生産を行うことが大きな損失に繋がるリスクが高まっています。
リードタイムを短縮し、ニーズに合わせた量を適宜生産・販売できるようになれば、売れ残りや不動在庫の発生防止に繋がるでしょう。
リードタイムを短縮する方法
リードタイム短縮のメリットを解説しましたが、では具体的にどのような方法をとればリードタイムを短縮できるのでしょうか。
生産・作業計画・管理方法の見直し
各工程における無駄を洗い出し、その無駄を削減するとともに、プロセスの最適化を行います。
たとえば、製品開発において試作と検証に実物を使うのではなく、3D CADなどを用いて仮想的にシミュレーションを行えば、効率的に開発プロセスを進められます。
配送ルートの最適化
配送を外部企業に委託している場合、委託先の企業によって配送ルートが左右されます。配送にリードタイムがかかりすぎている場合には、配送先に応じて委託先を変えるなどの取り組みを行うと良いでしょう。
ただし、配送ルートの変更がコスト増加に繋がる可能性もあるため、コストをふまえた検討が必要になります。
効率化を図るためのシステム導入を検討する
生産機械やシステムを用いて業務効率化ができれば、そのぶんリードタイムの短縮が図れます。全体のプロセスを一連の流れで管理できるSCMツールなどの導入も効果的です。
人員の増加・人材育成の環境整備
人員の増加や作業員の熟練度の向上もリードタイムの短縮に繋がります。単純な人手が増えれば生産能力が向上しますし、作業員の熟練度が向上すれば作業を効率的に進められるとともにミスや手戻りの防止も図れます。
人員の増加には採用や雇用のコストがかかるため慎重に検討する必要がありますが、人材育成の環境整備は大きなコストをかけなくても取り組めるため、積極的に取り組みましょう。
ノウハウやナレッジの共有
さまざまな業種において、熟練の技術者が抱える暗黙知の継承が課題となっています。その暗黙知をノウハウやナレッジとして共有できるようになれば、従業員全体の技術力の底上げに繋がり、リードタイムの短縮を実現できるでしょう。
ノウハウやナレッジを共有する場としては、情報共有ツールの導入・活用が効果的です。
ナレッジ経営クラウド「Qast」で生産性の向上を図る
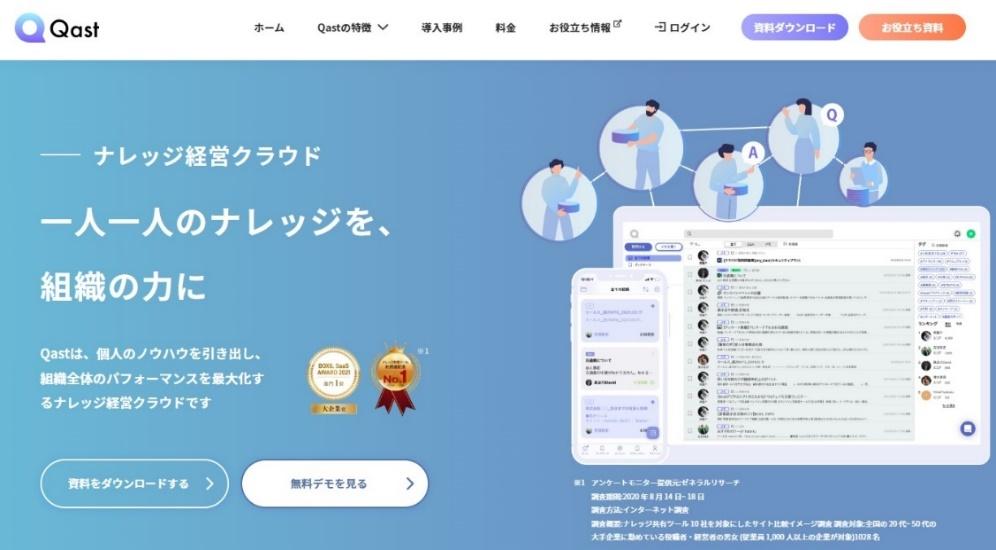
Qastは、社内における情報やナレッジの共有に適した「ナレッジ経営クラウド」です。シンプルで誰でも扱いやすい情報共有ツールのため、業界や職種を問わずさまざまな現場に導入できます。
テンプレートを作成して保存しておけば投稿作成の時間を短縮できるため、投稿者の負担を減らしながら情報・ナレッジ共有の場を整備できるでしょう。ファイル内の文字列検索に対応しているため、マニュアル整備やFAQ作成などにも適しています。
リードタイムの短縮を図るための情報・ナレッジ共有の基盤として、Qastをぜひご活用ください。
まとめ
リードタイムとは、各工程の始まりから終わりまでにかかる期間です。リードタイムの短縮を行えば、在庫管理の適正化や機会損失の現象、業務効率化に繋がります。
情報共有ツールも上手に活用しながら、リードタイムの短縮や適切な管理をぜひ実現してください。