7つのムダ「かざふてつどう」とは?それぞれの意味や対処法・解消法について紹介
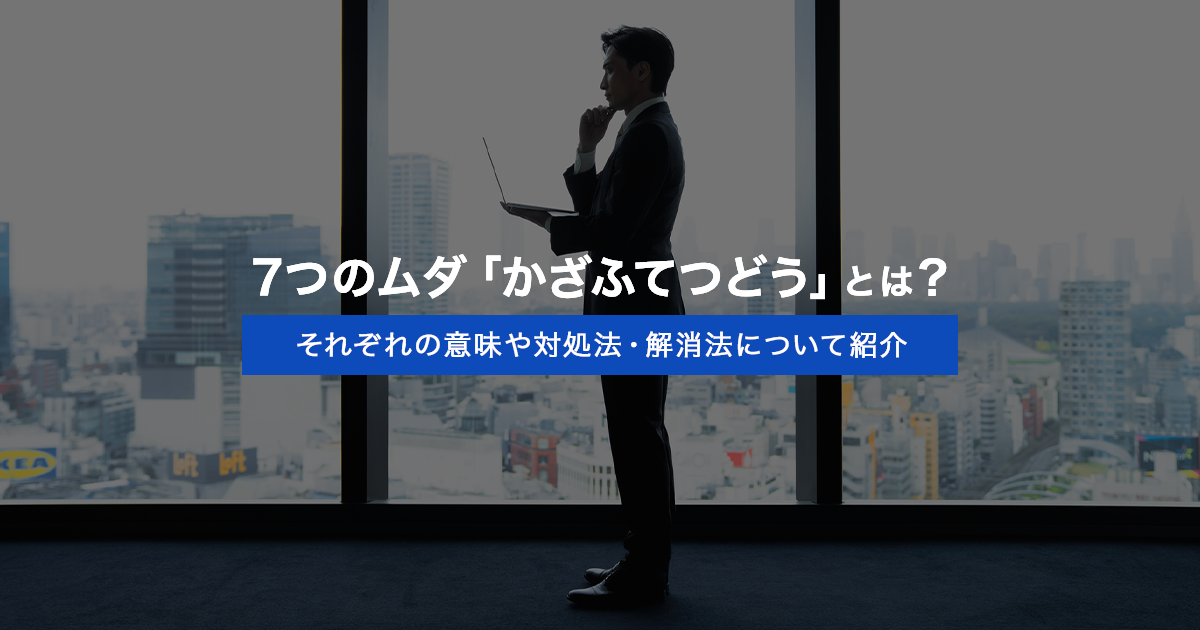
多くの製造業で人材不足が叫ばれる昨今、ムダを改善して効率的に作業を進めることがますます重要となっています。
しかし、どういう切り口でムダを見直せば良よいかわからず、場当たり的な改善にとどまっている現場も多いでしょう。
ここでは、製造業での現場改善に役立つ「7つのムダ」の視点や、それぞれの対処法を解説します。
目次
7つのムダとは?
まずは、製造業で注目されている「7つのムダ」とは何なのか、なぜ「7つのムダ」が生まれるのかを解説します。
7つのムダの定義
「7つのムダ」とは、現場作業において発生するムダの典型的な7つを挙げたものです。
具体的には「加工のムダ」「在庫のムダ」「不良・手直しのムダ」「手待ちのムダ」「造りすぎのムダ」「動作のムダ」「運搬のムダ」を指します。
7つのムダの視点で現場作業を見直すことで、現場に潜むムダを漏れなく洗い出せるようになります。
7つのムダが生まれた背景
7つのムダは、トヨタの生産方式から生まれた考えの一つです。近年のモノづくりの現場では顧客ニーズに柔軟に対応することが求められており、いかに顧客ニーズにあわせた製品を効率的に供給できるかが重要となります。
現場にムダがある状況では、顧客に製品を提供するまでに時間がかかる、コストがかかりすぎて新しい製品開発に投資できないなどの問題が生まれ、結果として顧客ニーズにあわない「売れないモノ」を作ることに繋がってしまいます。
7つのムダは、現場のさまざまなコストを削減し、顧客ニーズに応えられる現場づくりに役立つ視点として、現在では多くの製造現場で活用されています。
製造業における7つのムダ「かざふてつどう」とは?
製造業における7つのムダは、それぞれの頭文字を取って「かざふてつどう」とも呼ばれます。
それぞれのムダの意味や対処法・解消法を解説します。
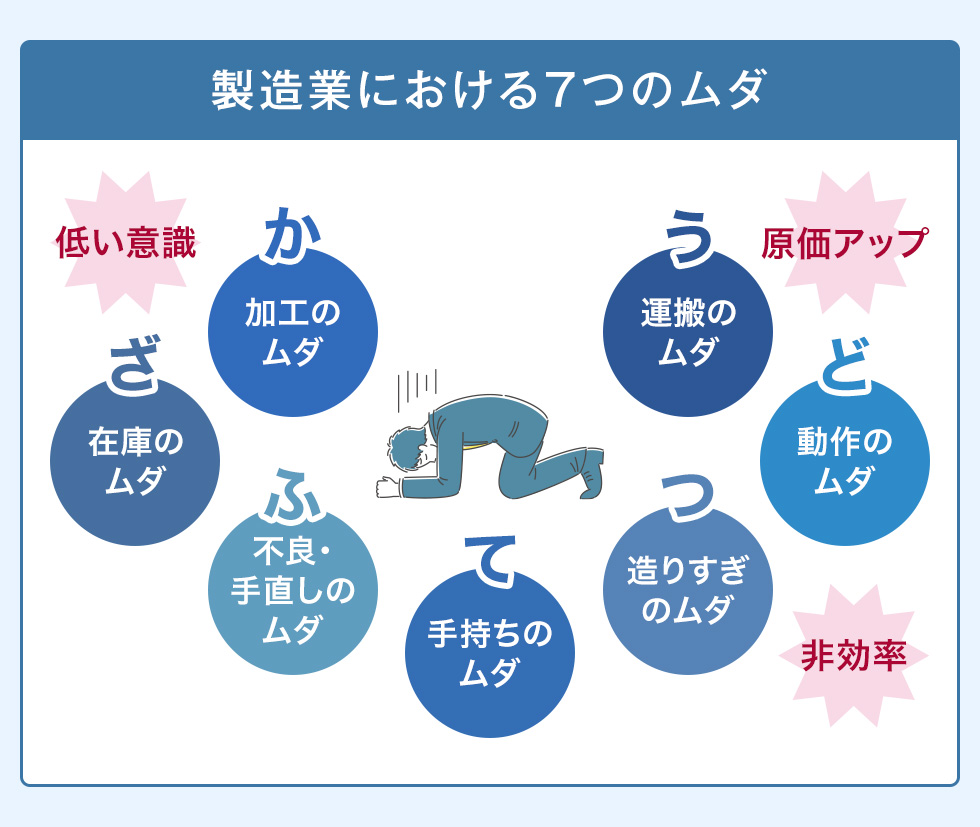
加工のムダ
加工のムダとは、製品の加工や品質検査作業などの工程におけるムダを指します。
加工は省くことのできない工程のため、見直す余地がないように思われがちですが、本来必要のない作業や検査が慣習的に残っていたり、工程間のロット情報の照会に時間がかかっていたりといったムダが発生している場合があります。
対処法・解消法
加工のムダを取り除くには、製品が出来上がるまでの加工工程をフローとして可視化し、不要な作業を洗い出す必要があります。
ポイントは、作業項目だけでなく、作業をどのように行っているかの詳細を洗い出すことです。加工工程の細かな作業を洗い出し、不要な作業が入っていないか、必要な作業でもより効率的に進める方法はないかを検討しましょう。
在庫のムダ
在庫のムダとは、不要な在庫を抱えることで生まれるムダを指します。
現場における在庫には、原材料や部品、仕掛品、完成品などが挙げられ、いずれも保管スペースや在庫管理のコストがかかります。顧客の注文に対して迅速に製品を出荷できることは重要ですが、在庫を抱え過ぎればその分コストが増加し、利益が減る原因となります。
対処法・解消法
在庫のムダを解消するには、システムを導入した管理が有効です。システムで在庫管理できれば、在庫数を確認しながら受発注ができ、受注量に応じてスムーズに発注を行えるようになります。過度な在庫を抱えなくても効率的に製造を行えるため、ムダな在庫コストを削減できます。
不良・手直しのムダ
不良・手直しのムダは、不良品による製品ロスや造り直し、手直しにかかるムダを指します。
製造において不良品はつきものですが、不良品の数が多くなればそれだけ利益が減少します。また、顧客に出荷した後に不良が発覚すれば、顧客の信頼を失う、高額な賠償金を払うなどのトラブルを生む点にも注意が必要です。
対処法・解消法
不良・手直しのムダには、徹底した品質管理が必要です。作業を標準化して誰でも同じ品質で作業できるようにすると同時に、品質検査により不良品を着実にはじくようにしましょう。
しかし、標準化した作業や機械での作業でも、一定数の不良品は出てしまうものです。不良品が出た原因を特定・分析するためにも、製造情報を管理できる仕組みやシステムを整備しましょう。
手待ちのムダ
手待ちのムダとは、作業員が待機状態にならざるを得ず、作業が止まってしまうムダを指します。
製造業では稼働率が重要な指標となりますが、手待ちのムダは稼働率低下の大きな要因となります。稼働率低下を防ぐためにも、工程間をシームレスに繋ぎ、待ち時間を減らすことが大切です。
対処法・解消法
手待ちのムダの削減には、前後の工程を考慮したフローで作業を組むことと、作業を標準化しておくことが重要です。前後工程の把握と標準化ができれば、前後の工程で待ちが発生する場合には待ち時間を極力減らすよう作業者をアサインする、特定の作業者だけが作業未完の場合には完了した作業者をアサインして協力して作業するなど、手待ちのムダを最小限にできるでしょう。
造りすぎのムダ
造りすぎのムダは、製品を造りすぎることで生まれるムダです。
造りすぎのムダは、在庫のムダや運搬のムダなど他のムダにも繋がるため、是正効果が大きいムダです。ムダを見直す際には、まず造りすぎのムダを見直しましょう。
対処法・解消法
造りすぎのムダを解消するためには、受注量や在庫数、生産量などの製造情報を把握することが必要です。製造情報を細かく把握できれば、必要なものを必要な時に必要な分だけ生産できるようになります。システムを導入して全体の製造情報を可視化しつつ、適正な製造量が保たれるようにしましょう。
動作のムダ
動作のムダは、作業員の不要な動作によって生まれるムダです。たとえば、原材料が保管されている場所が遠くムダな移動が発生する、作業時にしゃがむ、立つといったムダな動作の繰り返しが発生するなどが挙げられます。
動作のムダは製造を非効率にするほか、従業員の負担増加にもつながります。労災を防ぐためにも、動作のムダを是正することは重要です。
対処法・解消法
動作のムダを解決するには、作業手順の見直しや作業者へのヒアリングが有効です。作業手順にムダな動作が必要となる工程がないかを、実際の作業者が負担と感じていることと照らし合わせつつ確認することで、動作のムダ削減につながります。
作業が標準化されていないことも動作のムダが生まれる要因になるため、マニュアルの整備や研修の実施も重要な対策になります。
運搬のムダ
運搬のムダは、不必要なモノの移動によって生まれるムダです。ムダな仮置き・積替えが発生し余計な時間がかかっている、配送ルートが不適切で余計な配送費がかかっているなどが運搬のムダにあたります。
対処法・解消法
運搬のムダ削減には、造りすぎのムダや動作のムダなど他のムダとも関連しているため、他のムダを含めた全体的な視点での見直しが必要です。他のムダを含めて最適化を図れる設備や作業者の配置、レイアウトを検討するとともに、配送ルートなどモノの流れを定期的に見直すようにしましょう。
ムダを生まない仕組み作りが大切
現場のムダ削減において重要なのは、ムダを生まない仕組み作りです。ムダを生まない仕組み作りにおいて重要なポイントを3つ解説します。
自動化できる部分はないか考える
作業において自動化できる作業・できない作業の仕分けを行いましょう。システムや機械で自動化できる部分を自動化すれば、多くのムダ改善につながります。システムや機械の導入にはコストがかかるものの、長期的な視点で見れば大きなメリットが得られます。
作業フローを見直す
作業フローを可視化し、見直しを行いましょう。作業フローの可視化はムダの削減に不可欠です。当たり前の作業として普段は気にしていなかった作業でも、フローとして可視化することでムダが見えてくる場合もあります。まず現状の可視化から始めると良いでしょう。
スムーズな情報共有が行える体制を整える
ムダの削減には情報共有が有効です。スムーズな情報共有は、現場の可視化や作業の標準化、効率化、生産性向上に繋がります。スムーズな情報共有ができるようツールを導入しておけば、現場の声をヒアリングする際にも役立つでしょう。
ツールを利用する際に注意が必要なのは、作業者がツールを使いやすいかという点です。シンプルで誰でも使いやすいツールを導入すれば、スムーズに情報共有が行われる基盤を整備できます。
そこでおすすめしたいのが、社内におけるナレッジ・情報共有や社内ポータルサイトに適したナレッジ経営クラウド「Qast」です。Qastを導入すれば、スムーズな情報共有の基盤を整備できるとともに、作業の標準化やナレッジの蓄積にも活用できます。
現場のムダを見直す際には、ぜひQastの導入をご検討ください。
まとめ
7つのムダとは、現場作業で生まれる「加工のムダ」「在庫のムダ」「不良・手直しのムダ」「手待ちのムダ」「造りすぎのムダ」「動作のムダ」「運搬のムダ」の7つを指したもので、それぞれの頭文字を取って「かざふてつどう」とも呼ばれます。それぞれの要素でムダを見直せば、現場のムダを漏れなく洗い出せるでしょう。
いずれのムダにおいても、改善に重要なポイントは、作業フローの可視化と見直し、自動化、ナレッジ・情報の共有と蓄積の3つです。ここでご紹介した3つのポイントを参考に、現場の7つのムダをぜひ見直してみてください。